How Are Planes Made: From Blueprint to Sky – The Journey of an Aircraft
28 October 2024
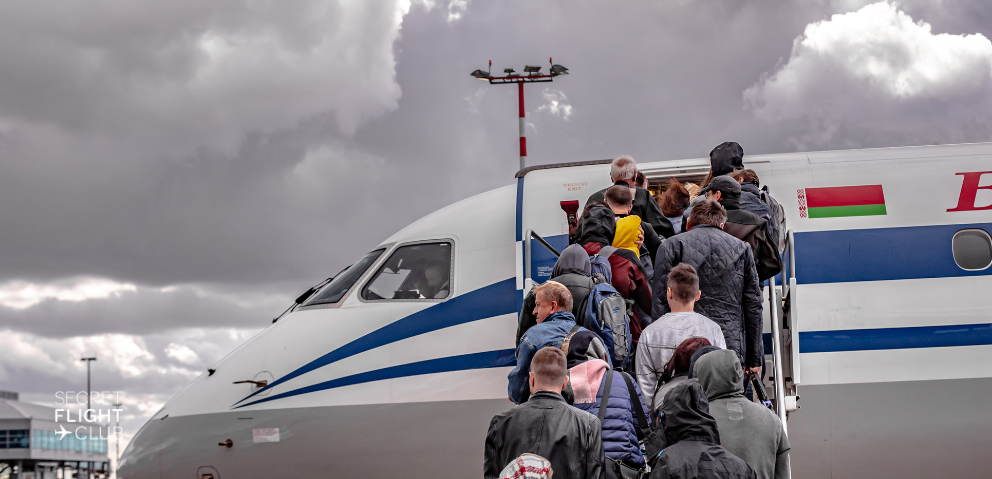
The journey of an aircraft from concept to reality is a marvel of modern engineering. How are planes made? This complex process involves meticulous planning, cutting-edge technology, and skilled craftsmanship. From the initial aircraft design process to the final assembly, each step is crucial in creating these magnificent machines that transport millions of passengers across the globe every day.
This article explores the fascinating world of aeroplane production, delving into the various stages of manufacturing. We'll look at how Boeing planes are made, examine the materials used in construction, and discuss the intricate systems that bring an aircraft to life. You'll gain insight into what planes are made of, how to build a plane, and the rigorous testing procedures that ensure safety in the skies.
Blueprint to Reality: The Design Process
The journey of an aircraft from concept to reality begins with a meticulous design process. This process is divided into three main stages: conceptual design, detailed engineering and 3D modelling, and prototype development and testing. Each stage plays a crucial role in bringing an aircraft from blueprint to sky.
Conceptual design and feasibility studies
The conceptual design phase is the foundation of aircraft creation. During this stage, designers and engineers work together to create rough sketches of various possible configurations that meet the required specifications. They consider multiple factors such as aerodynamics, propulsion, flight performance, structural systems, and control systems.
The shape of the aircraft's fuselage, wing location, and engine size are all determined at this stage. Designers aim to achieve a design that satisfies all the aircraft's requirements while optimising for factors like weight, fuel efficiency, and passenger comfort.
Feasibility studies are conducted to assess the viability of the project. These studies consider economic factors, market demand, and technical feasibility. They help determine whether the proposed aircraft design is commercially viable and technically achievable.
Detailed engineering and 3D modelling
Once the conceptual design is finalised, the process moves to detailed engineering and 3D modelling. This stage involves refining and optimising the conceptual design to fit within the necessary parameters.
Engineers use advanced computer-aided design (CAD) software to create detailed 3D models of the aircraft. These models allow for precise calculations and simulations, helping to identify and resolve potential issues before physical prototypes are built.
3D modelling has revolutionised the aircraft design process. It allows engineers to test different materials and designs without creating actual prototypes, saving time and resources. For example, engineers can use 3D models to test how an aircraft responds to different weather conditions or performs across various terrain types.
Prototype development and testing
The final stage in the design process is prototype development and testing. This stage turns the detailed 3D models into physical reality, allowing for hands-on testing and refinement.
Prototypes are crucial for testing new functionalities and demonstrating new capabilities. They allow engineers to simplify processes, check performance, improve safety, and reduce costs. During this stage, engineers may conduct wind tunnel testing and computational fluid dynamic calculations to analyse the aircraft's aerodynamics.
Prototype testing often involves a series of 'trial and error' cycles to obtain adequate solutions. This process requires a high level of agility and autonomy from the engineering team, as they need to respond quickly to make changes, even at advanced stages of development.
Throughout the design process, from conceptual sketches to prototype testing, the focus remains on creating an aircraft that meets all safety, performance, and efficiency requirements. This meticulous approach ensures that when a new aircraft takes to the sky, it's the result of years of careful planning, innovative design, and rigorous testing.
Materials and Manufacturing Techniques
The aerospace industry has witnessed a significant evolution in materials and manufacturing techniques, revolutionising how planes are made. Advanced composites and alloys have become the backbone of modern aircraft design, offering a quantum leap in performance, efficiency, and safety.
Advanced composites and alloys
Advanced composites have transformed the aviation industry, introducing a new era of aircraft design and capabilities. These engineered materials, made from two or more constituents with significantly different physical or chemical properties, create components with characteristics that surpass individual elements. In aerospace applications, high-strength fibres such as carbon, glass, aramid, and boron are typically embedded in a polymer matrix, often a thermoset or thermoplastic resin.
The adoption of advanced composites in civilian aircraft manufacturing has been nothing short of revolutionary. These materials offer significant weight savings compared to traditional metals, directly translating to improved fuel efficiency and increased payload capacity. Despite their lighter weight, composites often outperform metals in strength-to-weight ratio and fatigue resistance. They also provide design flexibility, allowing for more aerodynamic and efficient aircraft designs.
Aluminium alloys, titanium alloys, and steel continue to play crucial roles in aeroplane production. Aluminium alloys, when combined with other metals, significantly improve their mechanical properties while maintaining low specific weight. Titanium alloys possess high specific properties, good fatigue strength, and retain considerable strength at temperatures up to 400-500°C. Steel, despite its high specific density, remains valuable for castings of small components demanding high tensile strengths and stiffness.
Precision machining and forming
Precision machining and forming techniques have become indispensable in the process of how planes are made. These processes ensure the production of highly accurate and consistent parts to exact specifications, with accuracy down to the micrometre. The aerospace industry employs various machining processes, including CNC milling, CNC turning, and electrical discharge machining (EDM), each playing a crucial role in manufacturing complex and highly detailed parts essential for ensuring performance and safety in aircraft.
High-precision machining allows for the production of lightweight parts that are also strong, using materials such as aluminium and titanium. This process is much faster than other machining processes due to digital design and prototyping through CAD, allowing potential errors to be identified before physical manufacturing begins.
Additive manufacturing and 3D printing
Additive manufacturing, or 3D printing, has emerged as a game-changer in the aerospace industry. This technology allows for the creation of complex geometries with internal features required for cooling effects and weight reduction through newly optimised designs. The ability to produce parts with intricate internal structures and passages has revolutionised the manufacturing of components like fuel nozzles and hydraulic valve blocks.
Laser Beam Powder Bed Fusion (PBF-LB) and Electron Beam Powder Bed Fusion (PBF-EB) are the dominant metal additive manufacturing technologies used in the aerospace sector. These processes involve selectively melting metal powder one layer at a time from a 3D CAD model, producing nominally fully dense parts that undergo significant post-process finishing operations and rigorous quality checks.
The adoption of additive manufacturing has led to reduced costs, faster lead times, and vast improvements in flexible design and development methods. It has also contributed to lower CO2 emissions, both in manufacturing processes and end-use through lower fuel consumption, paving the way for greater sustainability in the aviation industry.
Building the Airframe
The construction of an aircraft's airframe is a complex process that involves various methods and techniques. The fuselage, which serves as the main body of the aircraft, is a critical component in how planes are made. It houses the crew, passengers, and cargo, while also providing a structure to which the wings and empennage are attached.
Fuselage construction methods
Modern aircraft manufacturers employ several methods to construct fuselages. One common approach is the semi-monocoque construction, which is preferred for building all-aluminium fuselages. This method begins with a series of formers that define the fuselage's cross-sections, held in position on a rigid fixture. These formers are then joined with lightweight longitudinal elements called stringers. The structure is covered with a skin of sheet aluminium, attached by riveting or bonding with special adhesives.
For some aircraft, particularly those designed for high-speed flight, monocoque construction is used. This method utilises stressed skin to support almost all loads, similar to an aluminium beverage can. The skin itself becomes the primary load-bearing structure, reducing weight and increasing aerodynamic efficiency.
Wing and empennage assembly
The wings and empennage are crucial components in how Boeing planes are made. The wing assembly process is intricate and involves numerous parts. For instance, the Airbus A380's wings contain nearly 500,000 parts alone. The assembly begins with the rear spar, which forms the backbone of the wing. Over several days, installation teams fit all the ribs, typically made of aluminium or carbon fibre composite materials, known for their strength and lightness.
Once the wing frame is complete, it is covered with massive aluminium panels that serve as its skin. Automated machines drill hundreds of thousands of holes in these panels to secure them to the frame. The completed wing can weigh up to 30 tonnes and stand as tall as a four-story building when lying on its side.
The empennage, or tail assembly, is equally crucial in aeroplane production. It typically consists of horizontal and vertical stabilisers, which provide stability during flight. The horizontal stabiliser controls pitch, while the vertical stabiliser manages yaw. These components are assembled using similar techniques to the wings, with a focus on precision and strength.
Structural integrity and stress testing
To ensure the safety and reliability of aircraft, rigorous structural integrity and stress testing are conducted throughout the manufacturing process. These tests are critical in understanding how planes are made to withstand various forces during flight.
Static and fatigue tests are among the most challenging campaigns in aircraft testing. They involve subjecting the airframe to forces that simulate real-world conditions, often over extended periods. For instance, tests might simulate an equivalent of 65 years of flight time to ensure the aircraft can operate safely for its intended lifespan.
Manufacturers use advanced technologies like strain gauges to measure the strain on aircraft components during flight tests. They also employ non-destructive testing (NDT) methods, which allow them to assess product and material qualities without causing damage. These techniques include ultrasonic testing, radiography, and infrared inspections.
The use of digital twins - virtual models that accurately reflect how materials or structures behave under various conditions - has become increasingly important in aeroplane testing. These models allow manufacturers to simulate conditions that may be difficult to replicate in real-world tests, providing a comprehensive dataset for analysis and design improvement.
Systems Integration and Final Assembly
The final stages of how planes are made involve intricate systems integration and assembly. This phase is crucial in bringing together all the components that make up a modern aircraft. The process begins with the installation of avionics and electrical systems, which form the nervous system of the plane.
Avionics and electrical systems are the backbone of modern aircraft. These systems include flight control computers, navigation equipment, and communication devices. In Boeing planes, the avionics are typically installed in a modular fashion, allowing for easier maintenance and upgrades. The electrical system is carefully integrated, with kilometres of wiring connecting various components throughout the aircraft.
Once the avionics are in place, the focus shifts to hydraulics and flight controls. These systems are essential for controlling the aircraft's movement in flight. Hydraulic systems power the movement of control surfaces such as ailerons, elevators, and rudders. The installation of these systems requires precision and thorough testing to ensure reliability and safety.
Flight control systems have evolved significantly over the years. Modern aircraft often use fly-by-wire technology, where electronic signals replace mechanical linkages. This technology enhances the aircraft's performance and efficiency. Boeing has been at the forefront of implementing advanced flight control systems in their planes.
The final step in the assembly process is the interior fitting and painting. This stage transforms the aircraft from a complex machine into a comfortable and aesthetically pleasing vehicle. The interior fitting involves installing seats, overhead bins, galleys, and lavatories. Each element is carefully designed to maximise passenger comfort while meeting strict safety standards.
Painting is not just about aesthetics; it also serves a protective function. The paint helps shield the aircraft's exterior from environmental factors and reduces drag. The painting process is highly specialised, often taking place in dedicated paint hangars. For Boeing planes, this process can take several days, with multiple coats applied to achieve the desired finish.
Throughout the systems integration and final assembly, rigorous testing is conducted at every stage. This ensures that all systems function correctly and meet the stringent safety standards required in the aviation industry. The testing phase includes comprehensive checks of all electrical, hydraulic, and mechanical systems.
The culmination of the aircraft production process is a series of ground and flight tests. These tests verify that the aircraft performs as designed and is ready for delivery to the customer. For Boeing, this final testing phase is a critical step in ensuring the quality and safety of their planes before they take to the skies.